The protagonist
Latteria Montello S.p.A.– Nonno Nanni MES Project
Nonno Nanni is one of the trademarks of Latteria Montello S.p.A., a company that processes over 60 thousand tons of fresh milk each year with a turnover of 90 million Euros, placing it among the market leaders in Italy in the soft cheese segment. Wholesomeness, tradition and quality: these are the key words that tell a story that began more than half a century ago when, in 1947, Giovanni Lazzarin, known as “Nanni,” first started a small dairy factory in the heart of the green pastures of Treviso. Today, the children and grandchildren of Nonno Nanni continue in the family tradition with the same commitment and the same age-old art but with advanced production technologies and processes.
The challenge
Needs
Following a very thorough software selection, Latteria Montello entrusted Qualitas Informatica and its NET@PRO MES proprietary software with the task of directing packaging activities towards maximum efficiency. Latteria Montello's product offering features a wide range of products (robiola, stracchino, spreadable cheese, etc.) under different trademarks and in various sizes and packaging options, therefore the need to improve department performance in terms of tooling times, waste reduction, traceability and activities planning and scheduling was of crucial importance for maintaining high competitiveness and meeting customer needs.
The project
Objectives
The main objectives of the project have been to:
- Increase department digitalization to obtain centralized management of orders and their electronic distribution on the lines (elimination of paper forms);
- Automatically send setup information to the entire line to avoid possible errors caused by manually entering data one device at a time, and allow real-time monitoring of the progress of orders;
- Automatically collect data such as: produced and used quantities, execution times, tooling times, machine downtimes, traceability, reject causes, etc.
- Control the storage and picking of semi-finished products and the situation of the semi-finished product contained in the cells;
- Automatically control the correct setup of the packaging line thus preventing the use of components that are non consistent with the order;
- Digitalize maintenance to speed up requests for action;
- Supervise the system when carrying out quality control to support controllers and facilitate line operators.
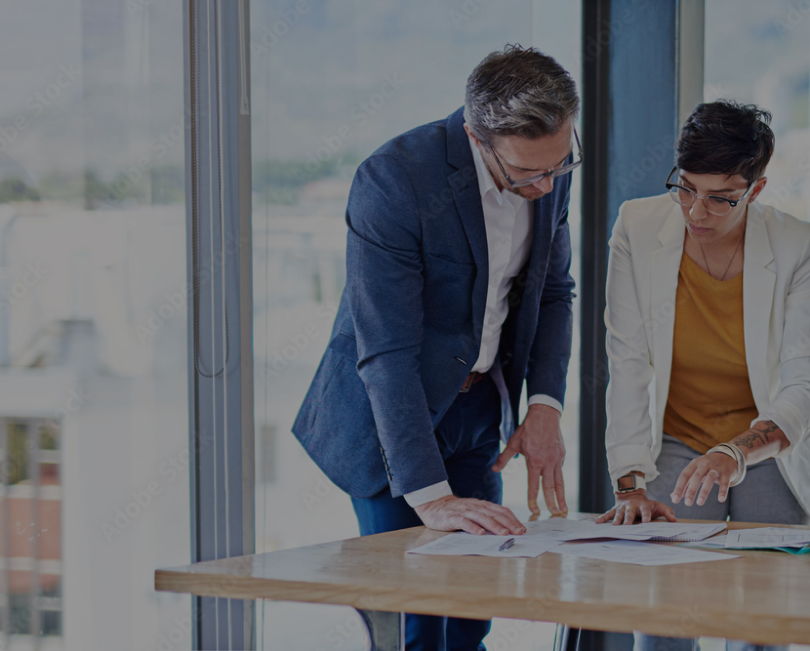
discover our connected services
.png?width=810&height=651&name=Rectangle%2067%20(1).png)