The protagonist
Polidoro S.p.A. MES Project
Polidoro originated in Schio in 1945 thanks to the work Aldo Polidoro and his brother Silvio who, from the very start, lit up the future with the production of acetylene tips used for lighting. Polidoro later went on to produce ceramic electrical insulators. In 1955, thanks to the constant search for innovative solutions that sets Polidoro apart, came the Radiantgas liquid gas heater, which recorded remarkable success on the market. Once again Polidoro proved to be a company able to read the future and seize the opportunities it was offered. The discovery of a number of natural gas deposits generated the need to adapt facilities already using gas to the use of methane. This was the input that pushed Polidoro to shift all studies and research to multigas burners. To date, Polidoro is a supplier of primary importance for most European makers of heating appliances. This explains the continuous growth this company has undergone in the last 4 years with a 60% increase in sales.
The challenge
The need to measure productivity
Already in 2006, Polidoro had begun analyzing production indicators. This was initially done on paper with productivity tables posted in the various departments, and later using Excel spreadsheets and counters. These solutions made it possible for each department to have an overall view of the performance of direct individuals and of the company's global efficiency, including indirect personnel. However, it did not allow operators to monitor production in real time, also making the recording of data, that was often too generic, quite burdensome. It was also difficult to systematically and objectively know the amount of time a machine had been down and the profitability of the machine when running. In addition, there was the need to understand if the focus on quality may have negatively affected productivity in general.
The collaboration between Qualitas Informatica S.p.A. and Polidoro S.p.A. began in 1998, when Polidoro implemented the NET@PRO MES in its factory.
The MES project started with the specific aims of a pilot department, which allowed it to:
– automatically control the progress of orders in real time;
– verify and keep track of component picking.
The results of the pilot MES project was a success: real-time monitoring of the production plant allowed Polidoro S.p.A. to reduce rejects, keep stocks low and improve efficiency.
In 2000, Polidoro S.p.A. ownership decided to extend the benefits of the NET@PRO MES software to the entire factory, to then later establish a continuous collaboration making Qualitas Informatica a key partner for the company's success, so much so that, once again, the NET@PRO MES was chosen as the solution to two needs that Polidoro was facing:
1. measuring productivity;
2. managing maintenance.
The project
The need to manage preventive maintenance
In 2014, Polidoro found itself facing a growth in production and the need to supply customers in increasingly shorter times without compromising quality. This led the company to review its concept of planning and control of production equipment maintenance. In fact, initially, preventive machine maintenance was managed using Excel spreadsheet checklists, and maintenance requests from the departments were all on paper, thus resulting in a lack of department feedback on maintenance, making it difficult to record servicing operations in general. It therefore became necessary to implement scheduled and preventive maintenance and, once again, Polidoro found the answer to its needs in a Qualitas solution. The first step taken by Qualitas was to design a specific module able to manage a preventive maintenance plan that covered 540 machines.
The goals achieved with the NET@PRO MES
The MES (Manufacturing Execution System) project designed made it possible to obtain important benefits:
- Andon 2.0
- Instantaneous visualization of daily productivity
- Instantaneous visualization of OEE for every shift
- Calculation of the delay due to the recording of various machine stops
- Visualization of the various stops including setup
- Easy to read
- Simple and effective management of preventive maintenance plans
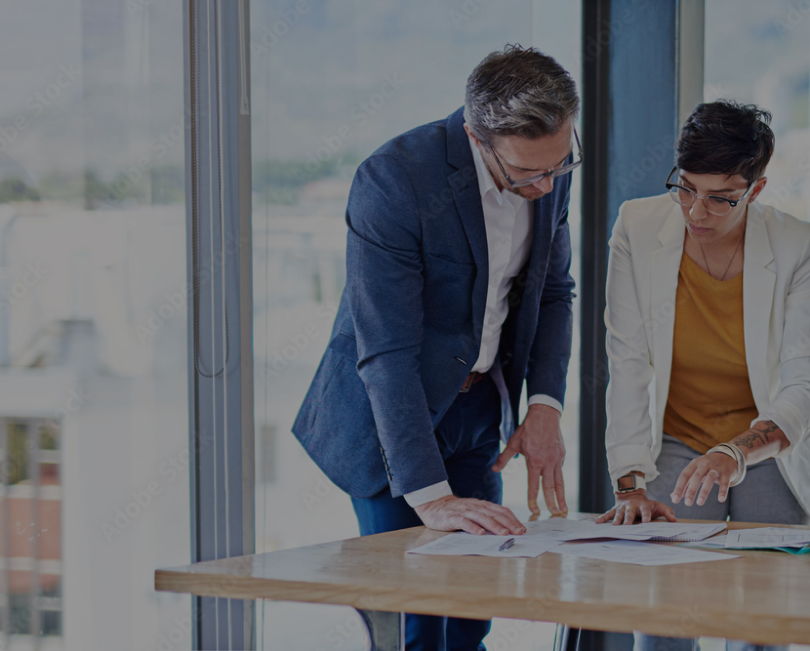
discover our connected services
.png?width=810&height=651&name=Rectangle%2067%20(1).png)